CONTINUOUS FILAMENT GLASS FIBRE
The continuous filament glass fibre industry is the cornerstone of the glass-based composite materials and technical textiles value-chains. The European production of continuous filament glass fibre is one of the smallest sectors of the glass industry in terms of tonnage. Glass Fibre Europe members produce approximately 1,000,000 tonnes of melted glass annually from 12 installations operating in 9 countries in Europe (Discover more). The industry directly employs over 4,500 workers in the European Union and it supports hundreds of thousands of indirect jobs down the industry value-chains.
The European glass fibre industry, including manufacturers, distributors, and related industries, is an essential industry sector. (Discover more) It is the cornerstone of the glass-based composite materials value-chain, which accounts for 95% of the European total production of reinforced composite, and the technical textiles value-chain.
Glass fibre’s unique properties enable the production of wind energy, electric and electronic devices, and the development of sustainable solutions in a wide range of applications, such as transport and construction. Glass fibre is a versatile material which will be vital to the achievement of the twin transitions to a green and digital economy.
THE MANUFACTURING PROCESS
PRODUCTS

Roving

Chopped strand
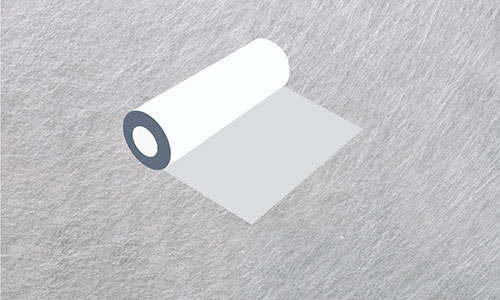
Mat / Veil
Yarns

PROPERTIES
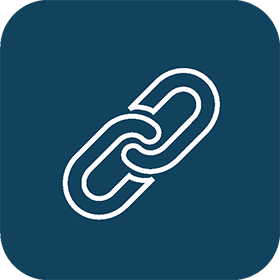
Mechanical
strength
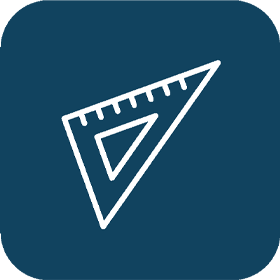
Dimensional
stability
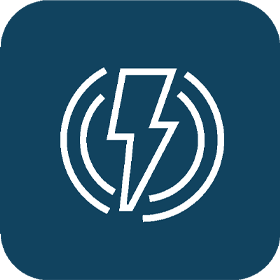
Electrical
insulation
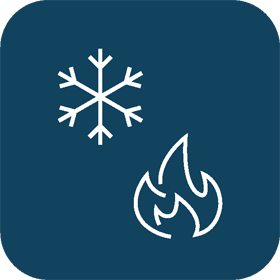
Low thermal
conductivity
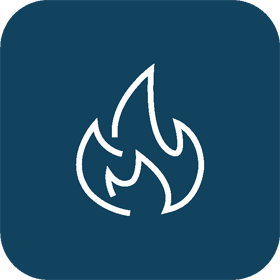
Fire
resistance
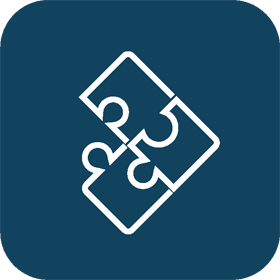
Compatibility with organic
matrices / materials
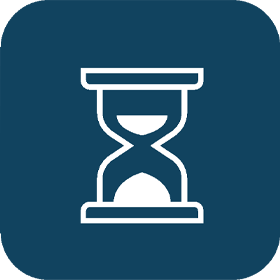
Durability

Dielectric
permeability
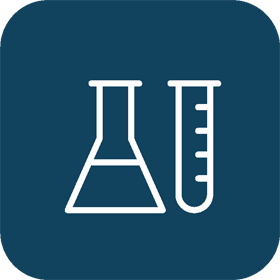
Resistance to
chemical agents
APPLICATIONS

Renewables:
Glass fibre made possible the advent of the wind energy industry, the largest contributor to renewable energy generation in the European Union, as an economically viable clean alternative to fossil fuel. Over the last decade, research and development enabled the development of increasingly larger lightweight wind turbine blades for improved energy generation efficiencies. Glass fibre is also present in other applications linked to the renewable industry. Glass fibre can be used as a reinforcement for plastics for the backing and framing of PV panels. It also contributes to the deployment of hydrogen as an alternative feedstock when used in reinforced stationary or vehicles tanks.
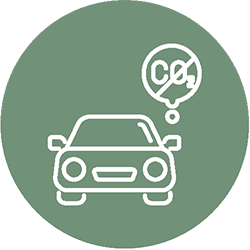
Transport:
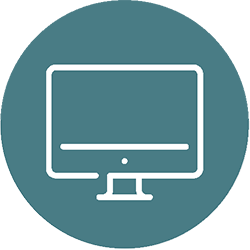
Electric & Electronics:
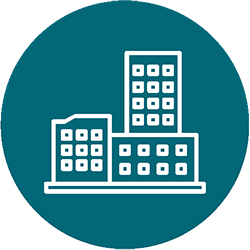
Building, Construction and Infrastructure:

Sports/Leisure:

Others:
Key industry data
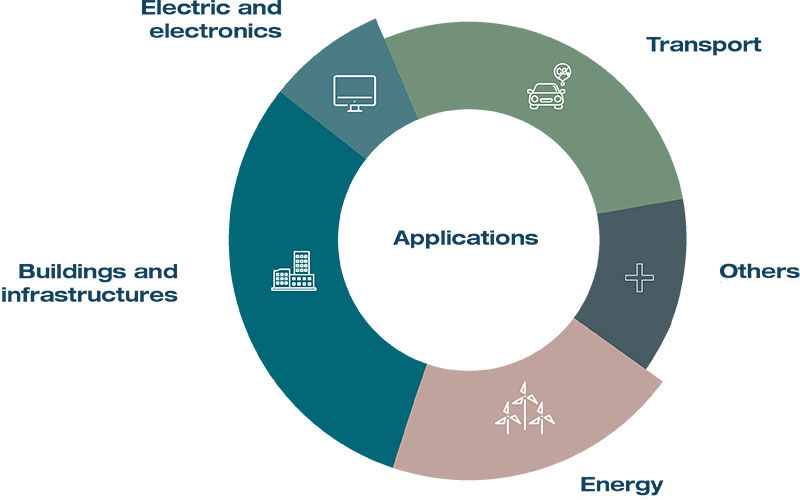
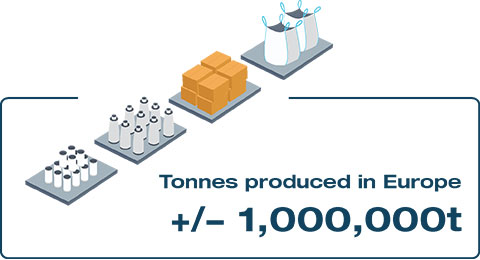
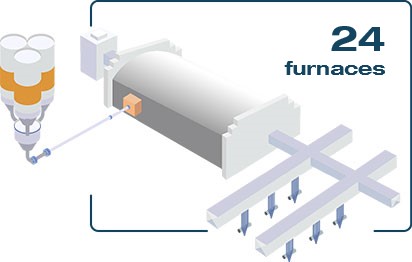
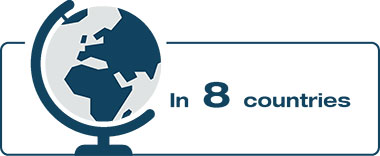
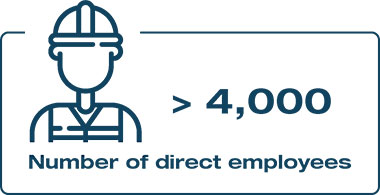
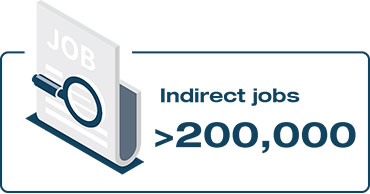
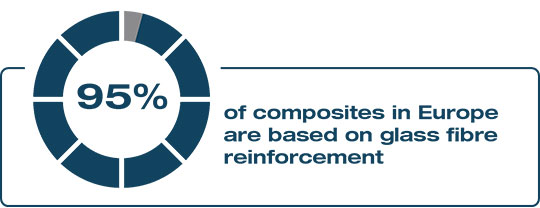